Irrigation advice: The causes of low voltage
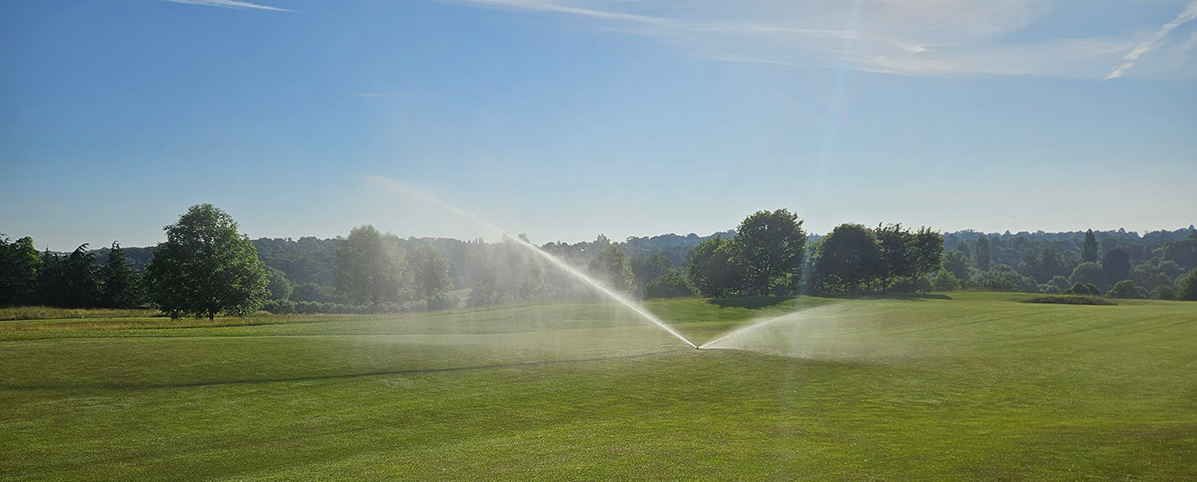
In his latest article looking at how to become an irrigation technician, John Kidson explores the causes and results of low voltage in a system.
*First published in the Greening Magazine written by John Kidson.
Within this issue I wish to cover the flow of voltage. Yes, this sounds strange but voltage over your cable network is key to any automated system working in the correct manner.
Let’s start with why we have voltage.
The voltage starts its journey from the irrigation controllers’ transfer, then over your cable network and in most cases via different cables, commonly called zones.
The irrigation controller will either have a consent voltage over the cable network or only voltage when in operation. This will depend on the brand of the controller.
Most common systems require a minimum voltage of 24 volts to operate a coil; these coils can either be on a solenoid valve or within a valve in-head sprinkler. I say 24v minimum, but you really need 28 / 30v due to a voltage drop once a coil is active. Most used coils say 24v and you can buy latching or non-latching – always best to double check when ordering replacements.
Your aim as an irrigation technician is to help the voltage over the cable network, the speed that the voltage can travel comes down to clean copper and good cable joints. An irrigation controller may start its journey with 34v, this can easily drop off the route due to bad joints, wet joints and cable issues. The issues then start to appear once you get near the minimum required voltage.
Low voltage issues
• Coils don’t operate or work intermittently.
• Random controller errors even though the stations work on a single test.
• Your coils / stations stop ahead of their planned run time.
Causes of low voltage
• Exposed copper.
• Wet conditions, which have submerged unprotected joints.
• A cable within the ground is damaged by machinery or is failing due to age.
• Bad cable joints in which, for example, copper does not touch copper.
• Distance. Each manufacturer has a maximum distance of a cable path.
As with water, you must help keep the flow going. Any cable joint early on within the cable path is a key point to check. Remaking copper joints and scrapping the copper clean can increase the voltage by a few volts, this doesn’t sound a lot, but you only have 30v or so to start with. Once your voltage has passed 50 joints or more, it only takes a few bad joints to lose 10 volts.
If you have the availability of cable within the ground or valve box, always try to strip the outer cable back more than required. This will allow for clamping when looking for decoder issues. I personally strip back two lengths of the cable with a yellow stripping tool.
For a strong cable joint, the best check you can undertake is to see if you can pull the cables out of the twisty part of a grease pod before putting the grease pod on.